CHAPTER 8: CULVERT HYDRAULICS |
8.1 CULVERTS
Culverts are hydraulically short drainage conduits placed in locations where the drainage network intersects
the transportation network (roads, railroad tracks). Culverts differ from bridges
in that they are much smaller; thus, there are many more
culverts than bridges. Culverts are designed to operate under gradually
varied flow; therefore, the principles
of Chapter 7 are applicable.
Culverts are designed to pass the design
discharge without overtopping of the superstructure.
The design discharge is derived from the
design storm,
which is based on hydrologic considerations.
The return period
(the reciprocal of the frequency) typically varies from
10 to 50 years (Ponce, 2008).
The longer the return period, the
greater the design discharge and, therefore,
the larger the required culvert size (Fig. 8-1).
Fig. 8-1 Large culvert at Yogurt Canyon, U.S.-Mexico
international border, California.
|
|
The flow in a culvert is a function of:
Cross-sectional size and shape,
Bottom slope,
Barrel length,
Roughness, and
Entrance and exit characteristics.
The flow in a culvert may be either (a) completely free-surface (open-channel flow), (b) completely
closed-conduit (pipe flow), or
(c) partially free-surface and closed-conduit flow. Headwater (HW)
is the depth of water above the culvert invert at the inlet.
Tailwater (TW) is the depth of water above the culvert invert at the outlet.
The design headwater and tailwater elevations are major
factors in determining whether the culvert flows partially full or completely full.
The design objective is to find the most economical design (i.e., the smallest culvert size)
that will pass the design discharge without exceeding a specified headwater elevation (Fig. 8-2). The design depends
on whether the culvert flow is under: (a) inlet control, or (b) outlet control.
Fig. 8-2 Large culvert crossing a
railroad embankment,
Tecate,
Baja California, Mexico.
|
|
8.2 INLET CONTROL
Culvert flow is under inlet control when the discharge depends only on the conditions at the inlet.
For example, assume a circular culvert of diameter D, length L, slope S,
headwater depth HW, and tailwater depth TW.
The first step is to
calculate the normal depth yn and the critical flow depth yc .
Then, the following situations are examined:
If yn <
yc , the flow in the culvert barrel is supercritical
and the tailwater has no influence on the upstream conditions (Fig. 8-3). Therefore, the headwater is solely controlled
by the conditions at the inlet.
Fig. 8-3 Culvert flow under supercritical conditions, with inlet submerged and outlet
unsubmerged.
|
|
If the flow is supercritical and the
TW > yn, a hydraulic
jump may form at or near the culvert outlet (Fig. 8-4).
Fig. 8-4 Culvert flow under supercritical conditions, with
inlet unsubmerged and outlet
submerged due to high tailwater.
|
|
Inlet control occurs when the culvert barrel is capable of conveying more discharge than the inlet will allow.
The control section is located just inside the entrance of the culvert. The flow passes through critical depth at the control
section and becomes supercritical downstream of the inlet.
Under inlet control, the culvert acts as an orifice or weir.
If the inlet is submerged, the flow condition resembles that of an orifice;
if the inlet is unsubmerged, the flow condition resembles that of a weir.
[If HW < 1.2 D, the inlet will be unsubmerged]. If the inlet is unsubmerged but the outlet is submerged,
a hydraulic jump will form inside the culvert barrel.
8.3 OUTLET CONTROL
Outlet control occurs under the following conditions:
When TW > 1.2 D, i.e., for high tailwater. In this case, the culvert barrel will be completely
full of water, resembling closed-conduit flow.
The headwater may be computed by applying the energy equation from the upstream (u/s) pool
elevation to the downstream (d/s) pool elevation.
The headwater is directly determined
by the tailwater elevation and the frictional characteristics of the culvert barrel.
-
When inlet and outlet are submerged.
-
When the culvert slope is mild
(subcritical flow) and both the headwater and tailwater
are less than the culvert diameter (HW < D; TW < D).
In this case, the best approach is to calculate the water-surface profile.
Figure 8-5 shows a schematic portrayal of flow rate as a function of
headwater energy under inlet and outlet control
(U.S. Army Corps of Engineers, 2014). Note that as the discharge increases from low to high,
at a certain level the flow changes abruptly more or less from inlet control to outlet control.
Fig. 8-5 Discharge
as a function of headwater energy under inlet and outlet control (U.S. Army Corps of Engineers, 2014).
|
|
8.4 CULVERT DESIGN
The following steps are followed in culvert design:
Assemble design data
Discharge,
Tailwater elevation, and
Slope of culvert barrel.
Choose the culvert characteristics
Cross-sectional shape (circular, square, rectangular, arch),
Dimensions (diameter, if circular),
Barrel length,
Kind of material (Figs. 8-6 and 8-7) (concrete,
corrugated steel,
corrugated aluminum, stone masonry), and
Type of entrance (square-edged or rounded).
Fig. 8-6 A set of
two culverts made with corrugated steel.
|
|
Ascertain the prevailing type of control (inlet or outlet), based on (a) headwater elevation,
(b) tailwater elevation, (c) diameter, and (d) slope.
If inlet control prevails, calculate the required
headwater elevation to pass the design discharge.
If outlet control prevails, calculate the required headwater elevation using (a)
the energy equation or (b) water-surface profile computations.
If the calculated headwater elevation is greater than allowed, choose a larger-size
culvert and repeat the process.
In some cases, it may not be possible to determine the type of control a priori.
In this case, both calculations are advised. The design type of control is that which results in the greatest headwater elevation.
Other design considerations in culvert design
Piping in the embankment surrounding the culvert,
Local scour at culvert outlet,
Erosion of fill material near the inlet,
Clogging with excessive debris, and
Provision for fish passage.
Fig. 8-7 A highway underpass featuring a
rectangular stone-masonry culvert.
|
|
Design Example
Design a culvert for the following conditions:
Design discharge: Q = 200 cfs.
Return period: T = 25 yr.
Barrel length: L = 200 ft.
Bottom slope: So = 0.01.
Culvert material: Concrete.
Manning's n = 0.013.
Inlet invert elevation: z1 = 100 ft.
Roadway shoulder elevation: Es = 110 ft.
Tailwater depth above outlet invert: TW =
y2 = 3.5 ft.
Freeboard: Fb = 2 ft.
Solution
The design elevation for the upstream pool is: Es - Fb = 110 - 2 = 108 ft.
Assume a circular concrete pipe, with square edge with headwalls.
Assume outlet control.
Assume that the hydraulic grade line (HGL) is at the elevation of the downstream pool.
Calculate the outlet invert elevation: z2 = z1 -
(So L) = 100 - (0.01 × 200) = 98 ft.
Calculate the downstream pool elevation: z2 + y2 = 98 + 3.5 = 101.5 ft.
Set up the energy balance (Fig. 8-8):
V12 V22
z1 + y1 + _____ = z2 + y2 + _____ + ∑hL
2g 2g
| (8-1) |
Fig. 8-8 Energy balance in culvert flow.
|
|
Assume V1 = 0, i.e., the velocity is zero in the upstream pool.
Assume V2 = 0, i.e., the velocity dissipates to zero in the downstream pool.
The head loss ∑hL is equal to the sum of entrance losses (with loss coefficient Ke), exit losses (with loss coefficient KE), and barrel losses.
Using the Darcy-Weisbach equation, the head loss is:
V 2
∑hL = [ (Ke + KE +
f (L / D ) ] _____
2g
| (8-2) |
From Table 8-1, assume
Ke = 0.5 and KE = 1 (Roberson et al., 1998).
Table 8-1 Loss coefficients in pipe entrance, contraction, and expansion.
|
Description |
Sketch
(Click on figure to display) |
Additional data |
Loss coefficient K |
Pipe entrance hL = Ke [V 2/(2g)] |
| r /d |
Ke |
0.0 |
0.50 |
0.1 |
0.12 |
> 0.2 |
0.03 |
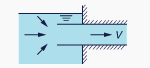 |
|
1.0 |
Contraction hL = KC [V22/(2g)] |
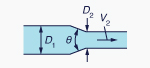 |
D2 /D1 |
KC θ = 60° |
KC θ = 180° |
0.0 |
0.08 | 0.50 |
0.2 |
0.08 | 0.49 |
0.4 |
0.07 | 0.42 |
0.6 |
0.06 | 0.32 |
0.8 |
0.05 | 0.18 |
0.9 |
0.04 | 0.10 |
Expansion hL = KE [V12/(2g)] |
| D1 /D2 |
KE θ = 10° |
KE θ = 180° |
0.0 |
| 1.00 |
0.2 |
0.13 | 0.92 |
0.4 |
0.11 | 0.72 |
0.6 |
0.06 | 0.42 |
0.8 |
0.03 | 0.16 |
The relation between Darcy-Weisbach friction factor f and Manning's n is
(Chapter 5):
8 g n 2
f = __________
k 2R 1/3
| (8-3) |
in which k = 1 in SI units, and k = 1.486 in U.S. Customary units.
In U.S. Customary units, with k = 1.486, and g = 32.17 ft/s2:
116.55 n 2
f = ____________
R 1/3
| (8-4) |
For a circular pipe: R = D / 4.
Therefore:
185.01 n 2
f = ____________
D 1/3
| (8-5) |
From Eq. 8-1,
the energy balance reduces to:
z1 + y1 = z2 + y2 + ∑hL
| (8-6) |
The head loss equation (Eq. 8-2) is repeated here for convenience:
V 2
∑hL = [ (Ke + KE +
f (L / D ) ] _____
2g
| (8-2) |
Replacing Eq. 8-5 in Eq. 8-2:
V 2
∑hL = [ 0.5 + 1.0 +
(185.01 n 2 L / D 4/3 ) ] _____
2g
| (8-8) |
Combining Eqs. 8-7 and 8-8:
V 2
6.5 = [ 1.5 +
(6.253 / D 4/3 ) ] _____
2g
| (8-9) |
The flow velocity is: V = Q / A. Therefore: V = 200 / A = 200 / [ (π/4) D 2 ]
The velocity head is: V 2 / (2g) = { 2002 / [ (π/4)2 D 4 ] } / (2g) = 1008 / D 4
Replacing the velocity head in Eq. 8-9:
1008
6.5 = [ 1.5 +
(6.253 / D 4/3 ) ] _______
D 4
| (8-10) |
Solving Eq. 8-10 by iteration: D = 4.38 ft. For design purposes, assume the next larger size: D = 4.5 ft.
With Q = 200 cfs, D = 4.5 ft = 54 in, enter Fig. 8-9 to find the ratio of headwater depth to diameter HW/D = 2.2, for the case of
square edge with headwalls (1).
Fig. 8-9 Headwater depth for concrete culverts with inlet control.
|
|
The headwater depth is: HW = (HW/D) × D = 2.2 × 4.5 = 9.9 ft.
The upstream pool elevation is: 100 + 9.9 = 109.9 ft. This upstream pool elevation is greater than 108 ft; therefore, it is too large.
The chosen D = 4.5 ft is too small. Try the next size: D = 5 ft.
With Q = 200 cfs, D = 5.0 ft = 60 in, enter Fig. 8-7 to find the ratio of headwater depth to diameter HW/D = 1.6, for the case of
square edge with headwalls (1).
The headwater depth is: HW = HW/D × D = 1.6 × 5.0 = 8.0 ft.
The upstream pool elevation is: 100 + 8.0 = 108.0 ft. This upstream pool elevation is the same as the design elevation; therefore, the design is now OK.
Calculate the normal depth using ONLINE CHANNEL 06: yn = 3.284 ft.
Calculate the critical depth using ONLINE CHANNEL 07: yc = 4.037 ft.
Since yn < yc, the flow is supercritical.
Since TW = 3.5 > yn = 3.284, there will be a small hydraulic jump at or near the outlet.
Since the flow is supercritical for most of the culvert length, it is concluded that inlet control prevails.
The design diameter is: D = 5 ft = 60 in. ANSWER.
|
QUESTIONS
What is a culvert?
What is the typical return period for culvert design?
When is a culvert under inlet control?
When is a culvert under outlet control?
List the hydraulic variables affecting culvert flow.
List other considerations in culvert design.
PROBLEMS
Design a circular concrete culvert with the following data: Q = 300 cfs;
inlet invert elevation z1 = 100 ft;
tailwater depth y2 = 4 ft;
barrel slope So = 0.02;
barrel length L = 200 ft;
Manning's n = 0.013;
roadway shoulder elevation Es = 112 ft;
upstream freeboard Fb = 2 ft.
The entrance type is square edge with headwalls (Fig. 8-10).
Use ONLINECHANNEL 06
to calculate normal depth and
ONLINECHANNEL 07
to calculate critical depth in the culvert.
Fig. 8-10 Typical culvert underpass.
|
|
Design a circular concrete culvert with the following data: Q = 500 cfs; inlet invert elevation z1 = 100 ft;
tailwater depth y2 = 4 ft;
barrel slope So = 0.01;
barrel length L = 200 ft;
Manning's n = 0.013;
roadway shoulder elevation Er = 115 ft;
upstream freeboard Fb = 2 ft.
The entrance type is square edge with headwalls. Use ONLINECHANNEL 06
to calculate normal depth and ONLINECHANNEL 07
to calculate critical depth in the culvert.
Verify the culvert design using ONLINECULVERT.
REFERENCES
Chow, V. T. 1959. Open-channel Hydraulics. McGraw Hill, New York.
Ponce, V. M. 2008. Questions and answers on the return period to be used for design. Online article.
Roberson, J. A., J. J. Cassidy, and M. H. Chaudhry. 1998. Hydraulic Engineering, Second edition, Wiley.
U.S. Army Corps of Engineers. 2014. HEC-RAS River Analysis System. Version 4.1, Hydrologic Engineering
Center, Davis, California.
http://openchannelhydraulics.sdsu.edu |
|
171117 20:30 |
|